Following on from the last two instalments on insulation, this month I’m going to talk about ventilation. Ventilation is an important part of any retrofit but I find it is often overlooked and misunderstood. Hopefully, I can help dispel it here!
A key part of any retrofit is reducing drafts, whether this is targeted specifically or a bi-product of insulation upgrades. It is important to distinguish between draughts and ventilation; draughts are unwanted air leakage and heat loss through the building fabric, for example around loft hatches, windows, doors, through holes and cracks, and so on. Ventilation is the removal of stale air from daily living, cooking, showering and so on, providing fresh air for us to breathe.
I come across lots of different ventilation setups and issues in my work. For example, in an old draughty property there might not be the need for any formal ventilation, as there is enough wind blowing through all the cracks and holes – so that stale air is removed and fresh air provided – albeit in a very uncontrolled way with a lot of heat loss. I have also seen plenty of cases of properties that may have had some insulation upgrades completed already, where the lack of formal ventilation has led to various issues like mould on the bathroom ceiling. In all cases, when upgrading the insulation, ventilation needs to be considered too.
So what are the options for ventilation?
Natural ventilation: The home is ventilated through a combination of air leakage and opening windows to remove stale air and provide fresh air. Though it would not meet new building regulations, this type of ventilation is common in older homes. The ventilation rate is difficult to control and relies heavily on the residents to open and close windows. It tends to result in under-ventilation in the winter months, when people are less inclined to open the windows. I wouldn’t recommend this in a home where any effort has been made to reduce draughts.
Intermittent extract fans: This system uses intermittent extract fans to remove stale air from the wet rooms, often set to run for 30 minutes when a light is turned in the bathroom, for example. If fresh air is planned for in this kind of system, it can be through trickle vents in the windows or through wall vents. Though often there may be no formal allowance for air supply. These systems work reasonably well in medium draughty buildings but can lead to over or under ventilation. As draughts are reduced, they are often inadequate.
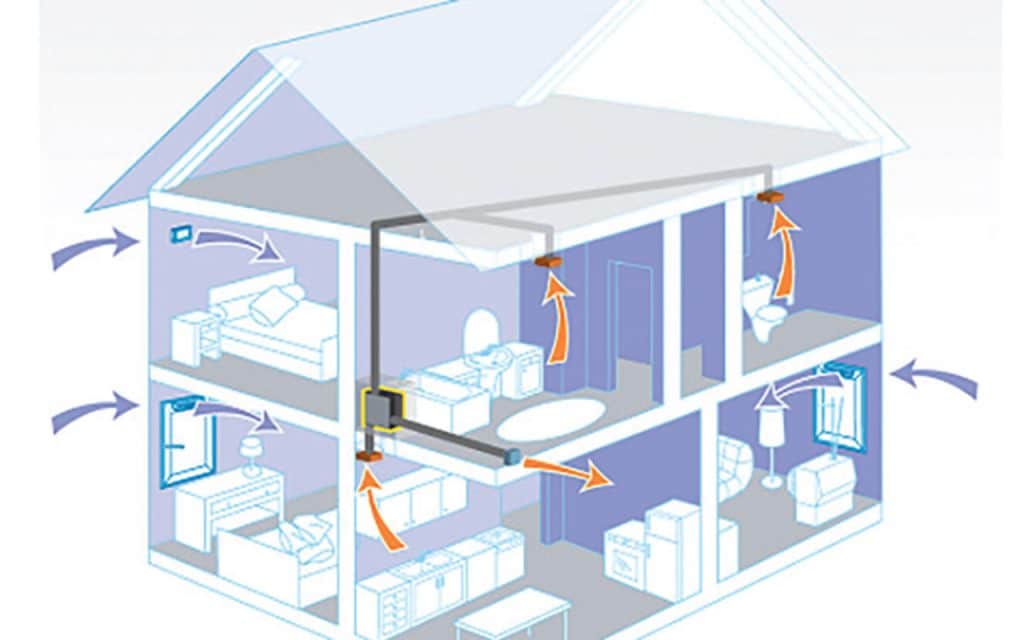
Centralised extract ventilation systems: There are some variations to these systems but the general principle is that you extract stale air continuously at a low rate. This is done via a central extract fan for the whole house which has ducting, (pipes) to extract points in all the wet rooms. Air intake is normally via trickle vents in the windows or through wall vents. This is referred to as mechanical extract ventilation or MEV. Demand control ventilation, (DCV) is very similar to MEV but can be boosted by certain triggers such as when humidity reaches a certain level in the room, hence the term demand control. These kind of systems can also use humidity-sensitive inlet vents through the walls or windows for air supply, only opening when fresh air is required. Some single room extract fans now also offer the same function, which can be handy in situations where routing ducting to a central location will be difficult. MEV or DCV is great for a retrofit where draughts are being reduced significantly and would be my choice on most projects. They are also useful where there is an existing problem with high levels of humidity, condensation or mould. The fans are extremely efficient to run and usually cost less than €20 a year to run in electricity. A small price to pay for indoor air quality.
Mechanical ventilation with heat recovery, (MVHR): This is the gold standard for ventilation, which originates from the German Passivhaus low energy building standard. The system comprises a centralised heat recovery unit with ducting to extract air from the wet rooms, as an MEV or DCV system would. The difference is that when this air is extracted, it is passed through a heat exchanger in the heat recovery unit before being dumped outside. This heat is then used to pre-heat incoming filtered fresh air, which is supplied to bedrooms and living rooms through a separate set of ducts. Heat recovery with a system like this can be up to 90 per cent. These kind of systems are more complex and expensive to install, particular in a retrofit where duct routes need to be found around the existing building structure to each room in the house. They are most effective in buildings, which have been made specifically airtight with very few draughts, to maximise the efficiency of the unit and balance the cost of the electricity to run the fans, (around €50 a year). The main situations where I would recommend MVHR are; on a deep retrofit and renovation project where the whole house is being stripped back inside and there is the opportunity to route the ductwork or in an airtight single storey bungalow where all the ducting may be able to pass through the attic.
If you would like to get in touch about anything in this article or your own retrofit project, feel free to reach out; ruairi@retrofurb.ie.